Система «бережливого производства», внедрённая на японских автозаводах в середине XX века, произвела настоящую революцию в организации работы предприятий. Она позволила увеличить производительность труда в разы и оказалась особенно оправданной в условиях глобализации и автоматизации. Вскоре её подхватили все продвинутые управляющие в развитых странах и сейчас практически любая уважающая себя компания работает по этой схеме.
Но эпидемия коронавируса и последовавший за ней кризис цепочек снабжения показал пределы возможностей системы, казавшейся безупречной. Как разрабатывалось «бережливого производства», в чем его суть, и какие корректировки ждут систему после пандемии — рассказываем в этом материале.
Подсмотрено в Америке
Если описывать смысл концепции одной фразой, то получится что-то вроде «производи ровно столько, сколько нужно, поставляй точно вовремя, не работай на склад». Сейчас многим это покажется невероятным, но но во времена, когда большая промышленность только создавалась, такие принципы показались бы всем странными. В начале XX века главной целью было производить быстро, много и дёшево. Корпорации делали рынку предложение, от которого невозможно было отказаться.
Развитие принципиально иной модели производства ассоциируется с Японией и корпорацией Toyota. Действительно, японские инженеры и управляющие ответственны за разработку этой концепции и начало её широкого применения, но на самом деле, как это часто бывает с восточноазиатскими ноу-хау, истоки идеи были подсмотрены на Западе.
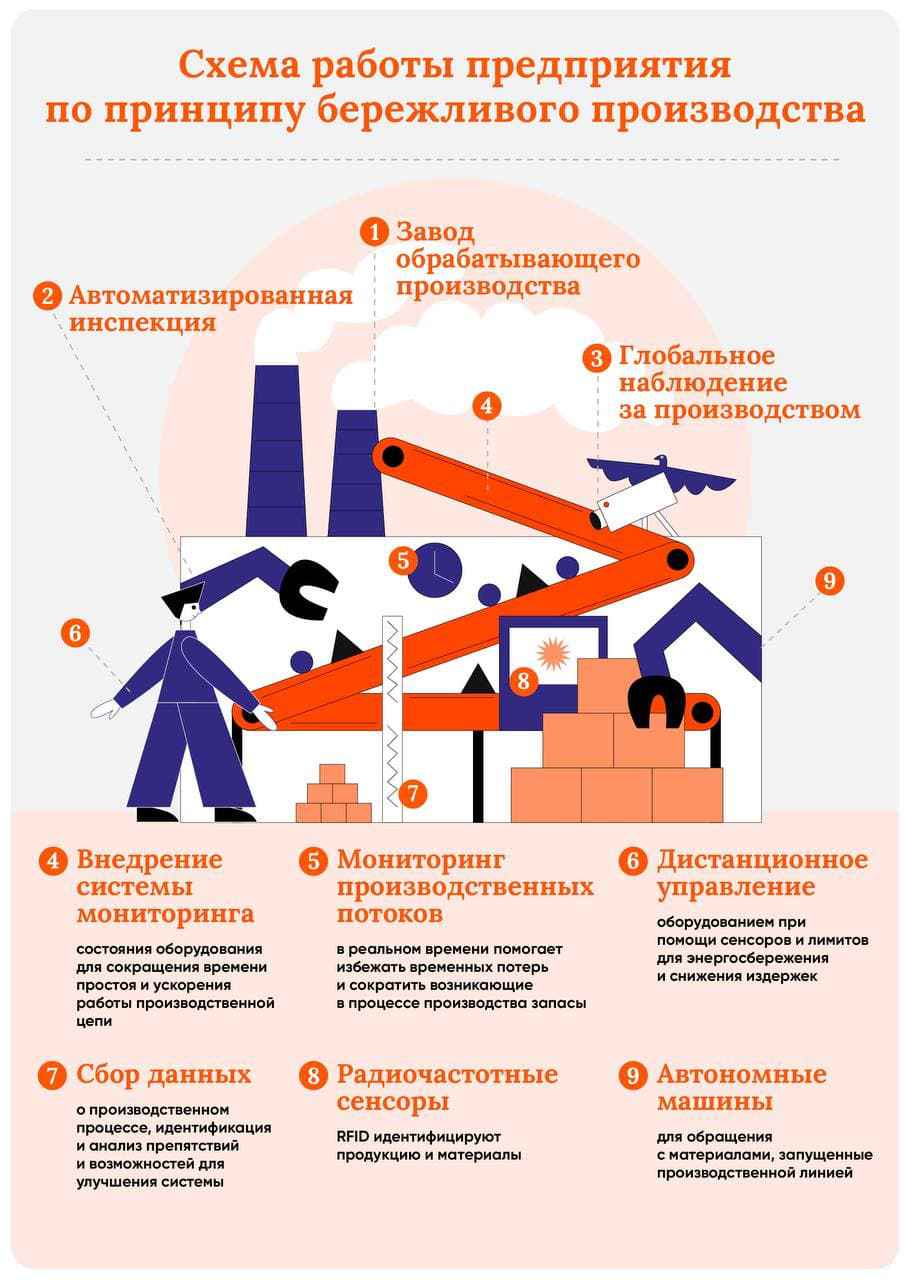
В начале 1950-х годов начальник механического цеха компании Тайити Оно побывал в командировке в США. Самое интересное, что он вынес из американского опыта, нашлось не на производствах Ford или GM, а в самом обычном супермаркете. Оно обратил внимание, что сначала покупатели разбирают продукты на полках, затем сотрудники магазина пополняют их ровно в том же количестве, в каком их раскупили, и такие же объёмы заказывают на складах.
Эта идея показалась крайне интересной в плане снижения издержек. Ведь если выпускать автомобили, ориентируясь на реально имеющийся спрос, то можно колоссально экономить деньги и ресурсы. Более того, ту же систему можно выстроить в отношениях между разными подразделениями вертикально интегрированного производства, и экономия вырастет в разы.
Почему такие идеи именно в Японии упали на благодатную почву? Тут можно выделить сразу несколько причин. Начнём с того, что в ходе Второй Мировой войны японская промышленность сильнейшим образом пострадала, а если выражаться менее дипломатично — была попросту стёрта с лица земли. Производственные системы в конце 1940-х — начале 1950-х создавались почти с нуля и из-за отсутствия нагрузки в виде устоявшихся традиций. Однако были и объективные проблемы, которые вынуждали искать новые подходы.
Во-первых, японские компании были бедны, чтобы позволить себе расточительство в виде «олдскульного» массового производства с созданием колоссальных запасов. Во-вторых, Япония — страна маленькая, её города – компактные и для складов с этими самыми запасами банально не хватало места. В-третьих, недостаток природных ресурсов требовал обращаться с ними максимально бережно и не тратить почём зря. В-четвёртых, спрос внутри страны был низким из-за крайней бедности послевоенной Японии. Следовательно, вариант снижения издержек за счёт эффектов масштаба, что прекрасно работало в богатой Америке, для Страны восходящего солнца был неприемлем.
Усилиями Оно и инженера Сигео Синго (тоже вдохновлявшегося примером США, правда, не практикой, а теорией, описанной, например, в книгах Фредерика Тейлора) была создана совершенно новая схема, получившая название «Производственная система Toyota» (Toyota Production System, TPS). Система в кратчайшие сроки дала всходы на заводах компании, позволив заметно снизить издержки, сократить запасы почти на порядок, а производительность труда — в полтора раза. Чуть позже её переняли и другие японские промышленники.
Начиная с 1960-х годов японское автомобилестроение стало стремительно завоёвывать американский рынок, что могло бы стать анекдотом ещё за 10 лет до этого. Однако американцам было не до смеха: японцы теснили их по всем фронтам, а после нефтяного кризиса 1973 года, когда большие американские авто резко потеряли в конкурентоспособности, стало совсем плохо. Разумеется, промышленники и экономисты в США немедленно заинтересовались, за счёт чего у японцев всё так хорошо получается — и знания и идеи потекли в обратном направлении через океан.
В конце 1970-х годов в нескольких американских журналах вышли статьи, описывающие японскую систему производства. В скором времени их начали внедрять автомобилестроители и другие промышленники. А в 1988 году молодой американский инженер Джон Крафчик в своей статье The Triumph of the Lean Production System впервые использовал закрепившееся название «Бережливая производственная система» (lean буквально переводится с английского как «худой, поджарый», в переносном смысле – «бережный, экономный»). С тех пор система далеко вышла за пределы автомобилестроительной отрасли, да и вообще промышленности, и стала использоваться компаниями всего мира, превратившись из ноу-хау в стандарт производства.
Тяни, не толкай
Ключевыми понятиями для описания бережливого производства являются японское слово kanban и английское pull. Kanban в переводе с японского означает «карточка» – карточками снабжались рабочие на заводах Toyota в 1950-е годы. С их помощью они сигнализировали в цеха, поставляющие для них материалы и комплектующие, чего и сколько им нужно.
Pull на английском языке означает «тянуть». В плане производства под этим термином подразумевается «вытягивание» данных о необходимых объемах поставок снизу вверх по производственной цепочке (или от конца к началу). Этот принцип противопоставлялся доминировавшему тогда в западной производственной системе принципу push (англ. «толкать»), когда производитель «выталкивает» на рынок определенное количество товаров, примерно ожидая, чего хочет рынок. В такой системе неизбежно довольно сильное затаривание складов, а значительная часть материалов может пропасть зря.
С принципом pull система стартует на уровне потребителя. «Вытягивание» предполагает, что товар производится не в планируемых в соответствии с ожиданиями о спросе количествах, а непосредственно по требованию потребителя или клиента. Дальше принцип распространяется уже на производственные цепочки — от выпуска конечной продукции до комплектующих и, наконец, материалов. Каждый цех требует от цеха-поставщика ровно столько материалов, сколько им нужно для производства нужного количества товаров в определённое время.
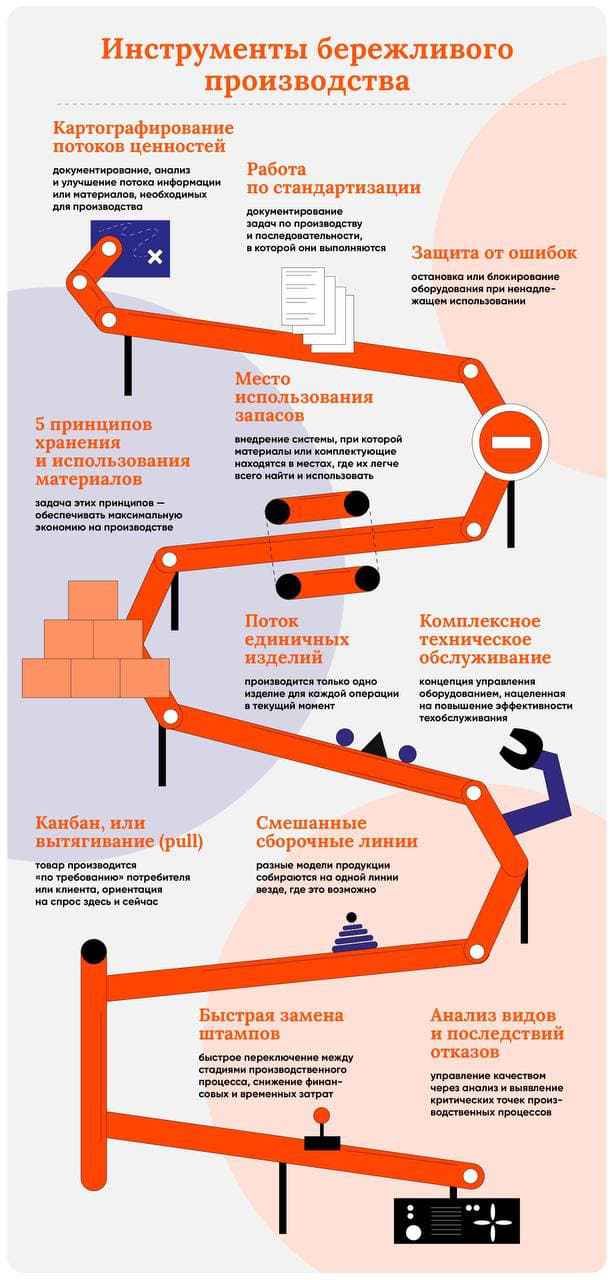
Ещё один ключевой элемент системы — это картографирование потоков ценностей (value stream mapping, VSM). Эта практика предусматривает документирование, анализ и улучшение потока информации или материалов, необходимых для производства продукта или услуги для потребителя. VSM дает возможность увидеть, где фактическая ценность добавляется в процесс, позволяя принимать решения по оптимизации общей эффективности производства.
Смешанные сборочные линии означают, что разные модели продукции собираются на одной линии везде, где это теоретически возможно. Как и другие понятия «бережливого производства», оно пришло из практики компании Toyota, первой начавшей сбор разных моделей автомобилей на одном конвейере.
Поток единичных изделий (one-piece flow production) предусматривает, что производится только одно изделие для каждой операции в текущий момент. Несколько изделий могут находиться одномоментно в процессе, но только одно в любой из операций. Таким образом сокращаются потери времени, когда остановок между производством продукции практически нет.
Визуальный менеджмент 5S состоит из 5 принципов хранения и использования материалов. Аббревиатура несёт в себе 5 японских слов — seiri, seiton, seiso, seiketsu и shitsuke, которые можно перевести как «сортируй», «располагай в порядке», «держи в чистоте», «стандартизируй» и «поддерживай» соответственно. Задача этих принципов — обеспечивать экономию материалов. Если каждый рабочий снизит объём отходов, мусора и брака на сумму 5 долларов в месяц (что как раз и достигается применением данных техник), то в масштабах корпорации издержки могут упасть на сотни тысяч долларов.
Бумеранг для Toyota
В условиях автоматизации и широкого применения электроники реализовывать концепцию бережливого производства стало особенно выгодно из-за облегчения контроля и «выпрямления» процессов производства. Более того, её принципы перешли в другие сферы экономики, например, в IT. Однако эпидемия ковида и последовавшие за ней экономические потрясения показали, что у системы есть свои слабые места и довольно острая критика.
Что произошло в 2020 году? Пандемия привела к локдауну на многих предприятиях и фактически сломала механизм поставок «точно-в-срок», который до этого удалось отладить практически как часы. Кроме того, беспрецедентное по масштабам вливание ликвидности в финансовую систему (фактически печатание денег центробанками) привело к росту спроса, причём до момента, когда предложение начало восстанавливаться. В экономике и промышленности случился двойной шок. Ситуация обострилась из-за дефицита контейнеров и резкого (в 10 и более раз) роста тарифов на морском транспорте.
Не добавила хороших новостей и сложившаяся именно у предприятий бережливого производства традиция работать с одним-единственным поставщиком каких-либо материалов и комплектующих. В «мирное» время это имело смысл, поскольку таким образом было значительно проще обеспечить синхронизацию поставок с нуждами предприятия. В кризис такая практика лишь резко повысила риски.
Классический пример — индустрия производства полупроводников, которая и сама оказалась в непростом положении, и «взяла в заложники» чуть ли не всю мировую экономику. В одночасье цены на микрочипы выросли в разы. Для компаний электронной промышленности (производителей смартфонов, компьютеров и комплектующих к ним, различных приборов) это было неприятно, но по-настоящему тяжёлый удар понесли автопроизводители. Дело в том, что компании, выпускающие чипы, оказались завалены заказами, и были вынуждены выбирать приоритеты. Неудивительно, что они предпочли электронщиков, которые заказывали у них больше и покупали более дорогостоящую продукцию. Автопроизводителям же было отказано.
В результате из-за деталей стоимостью в 10 долларов корпорации были вынуждены останавливать конвейеры с автомобилями ценой в десятки и сотни тысяч долларов. Автомобильные электронные устройства было невозможно купить ни за какие деньги — их просто не было на рынке. Ирония судьбы заключается в том, что одним из главных пострадавших оказалась Toyota, компания, впервые внедрившая принципы «точно-в-срок». В прошлом году корпорация сократила производство на 40%, а не далее как в январе и вовсе остановила рабочие процессы на всех своих заводах.
Если бы в глобальной экономике преобладало традиционное, «небережное» производство, проблема могла быть смягчена наличием существенных запасов, которые в прежние времена достигали показателей, на порядок больших, чем современные. Выпуск бы значительно увеличился даже в условиях разрыва производственных цепочек, и в большинстве секторов удалось бы избежать дефицита и резкого роста цен. Но запасов не было. Впоследствии компании начали в панике забивать склады материалами и комплектующими, но такие судорожные действия только усугубили дефицит.
По оценке экономиста Федеральной резервной системы США Хулио Ортиса, практики бережливого производства усугубили экономический спад примерно на 15%. Оценок воздействия на инфляцию не было, но здравый смысл подсказывает, что они могут быть намного больше.
Пандемия в целом заставляет мир пересматривать отношение к экономике. Среди экспертов появилось много сторонников возвращения к некоторым старым практикам и принятия принципиально новых — от более активной локализации производства до диверсификации цепочки поставок. Не исключено, что изменения постигнут и принципы бережливого производства. Разумеется, это не значит, что наработанный за последние 70 лет колоссальный и успешный опыт будет сразу отброшен. Но корректировки в сторону большей надежности и устойчивости неизбежны.